The Aquablast 1215 is the second largest of our standard wetblasting models, and is more suitable for degreasing and blasting medium sized components. The machine needs to be large enough to maneuver the largest overall component that needs blasting while taking into consideration ease of operation. The maximum turn table for this machine is typically 900mm.
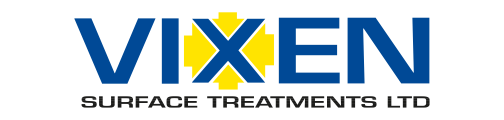
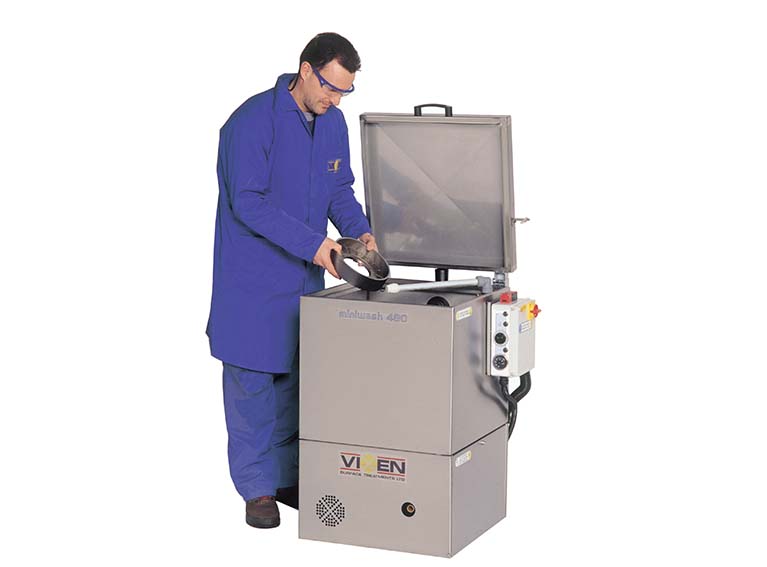

The Miniwash is ideal for small parts to be cleaned thoroughly automatically.
Detergent is sprayed with a fixed spray boom above, to the side and below the rotating mesh basket, giving components a thorough wash. After closing the lid, the timer is set to the desired wash duration and the machine automatically starts. During the wash cycle, the basket rotates and the components are cleaned quickly.
Due to the temperature of the detergent, the components flash dry in seconds at the end of the cycle. The Miniwash Degreasing Machine has been designed to operate in machining cells, allowing operators to batch wash their components efficiently.
Vixen Surface Treatments can offer customers portability to meet their washing and degreasing needs through the Miniwash degreasing machine.
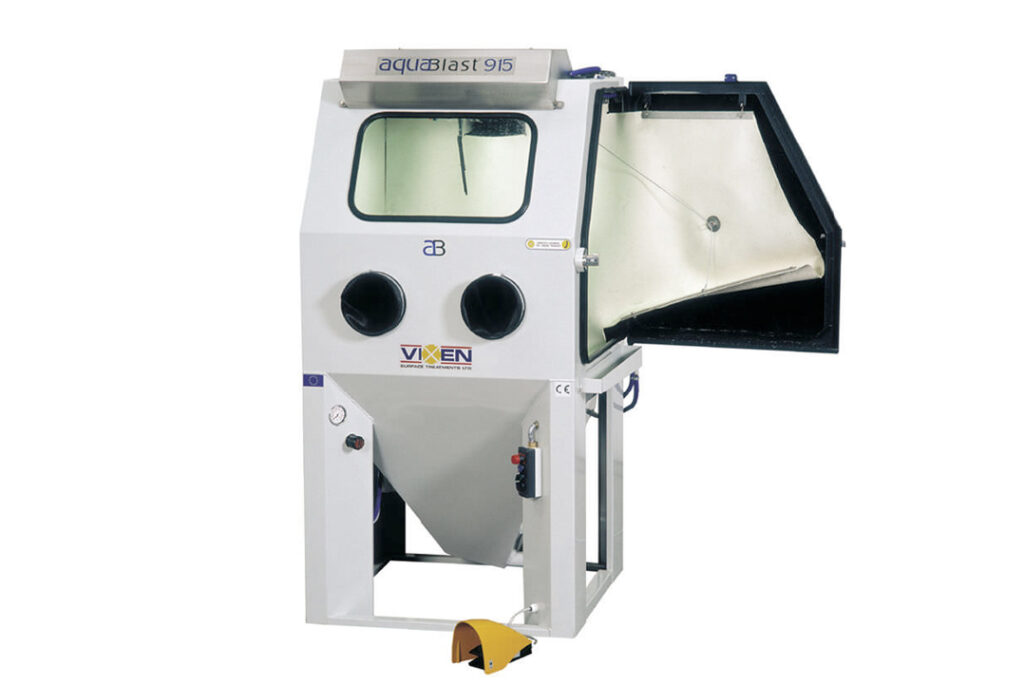

The Aquablast 915 is the smallest of our standard wetblasting models and is more suitable for degreasing and blasting smaller components with a maximum turntable of 600mm.
The water/media slurry is contained within the cabinet sump. Delivery of the slurry to the manual blast nozzle is via a glandless polyurethane pump and associated hoses located inside the machine.
Compressed air is added at the blast nozzle to accelerate the slurry and provide the cleaning effect. After contact with the component the slurry then drains back into the sump creating a re-circulating system. Fine broken down media and other contaminants are fed via an overflow to a sedimentation filter located at the rear of the cabinet.
The process cleans by flow not by impact, producing a ‘soft’ finish with the water acting as a lubricant which not only avoids media impregnation but also extends the life of the blast media.
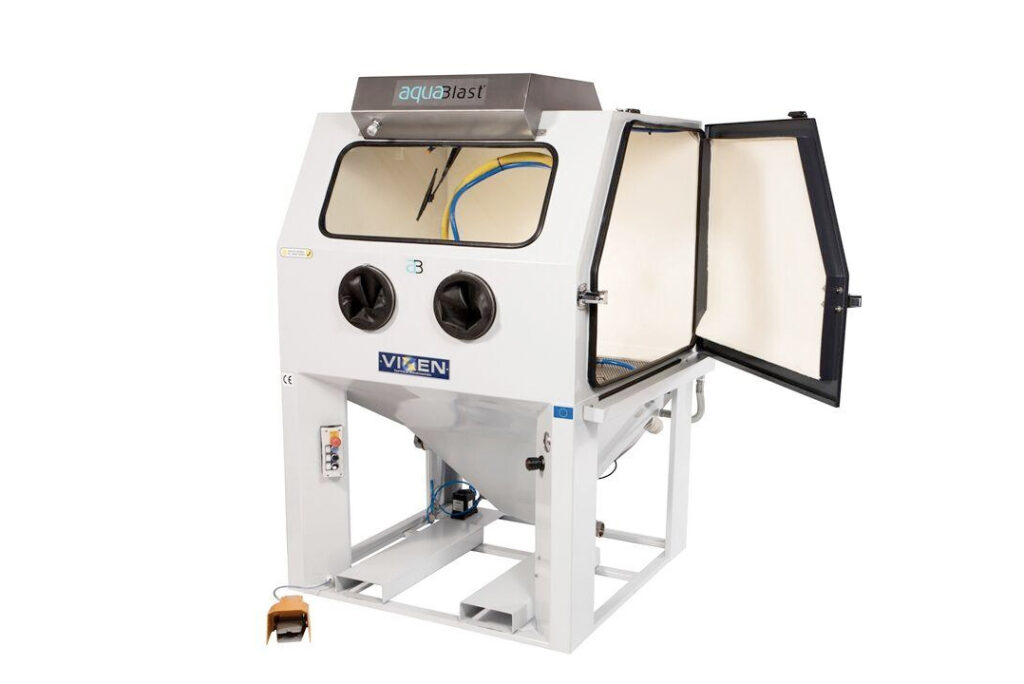



This machine blasts, washes and prepares alloy wheels in one quick and simple step ready for painting and lacquering. This process uses water mixed with abrasive to surface treat the alloy and provide an ideal surface for paint or lacquer to adhere to. The use of water ensures no media is impregnated onto the alloy wheel. The water also provides a washing action and does not strip the wheel back to bare metal. The wetblasting process used in the Aqua Wheelblaster does not need a specific room for siting, eliminates the risk of dust and combines all of the preparation process in one cabinet – ideal for the workplace.
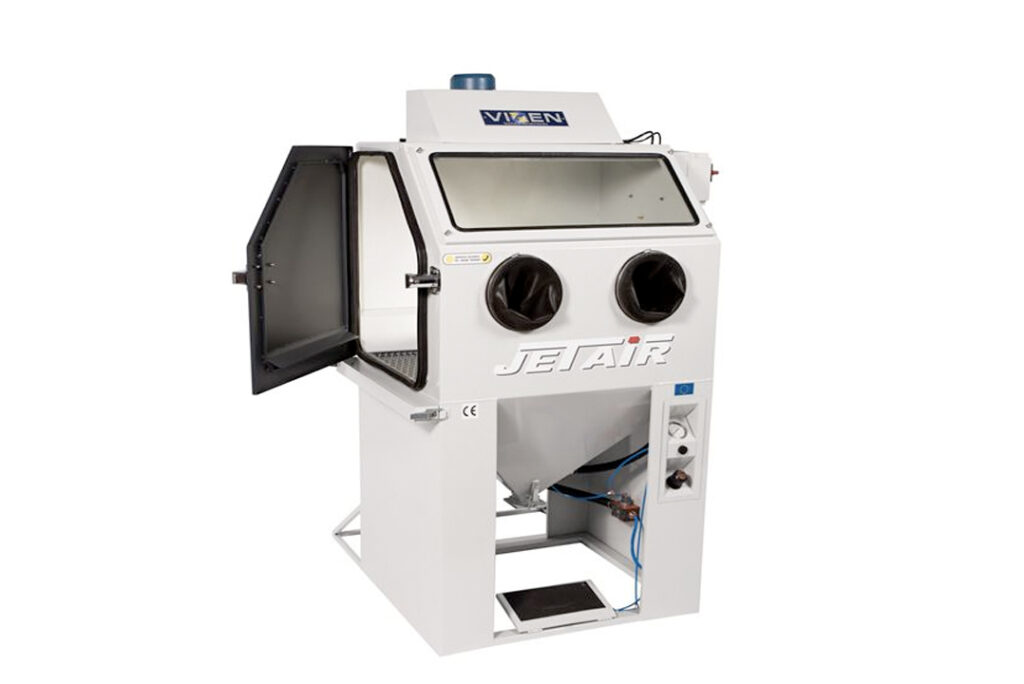

The halogen lighting and high performance cartridge dust collection/filtration system fitted to this model ensures maximum internal visibility, which is vital for yielding first-class results.
A standard Jetair machine uses the suction feed method during the blasting process. Compressed air is used to create a ‘venturi’ effect, where blast air is sucked up through the hopper of the cabinet to the blast gun and then propelled onto the surface of the component. The media then falls back to the hopper and is recycled.
Alternatively, Jetair machines can use a pressure operated blast system which increases the speed of blasting by up to four times and increases efficiency. These pressure pots are available in large and small sizes and are an optional extra in the Jetair range.


Jetwash machines are built entirely with stainless steel, inside and out. The hot wash spray machine uses a hot water and environmentally-friendly detergent. A double-skin construction with 18mm injected cavity insulation provides maximum insulation to the hot water, resulting in extremely strong build rigidity.
The Jetwash has been designed to automatically perform washing and degreasing on a wide variation of components. The process has three easy steps: load the basket, close the lid and then press start.
The cycle is adjustable and resets automatically each time the lid is opened. The wash basket remains stationary while the spray boom revolves around it, ensuring that delicate components will not get damaged by movement.
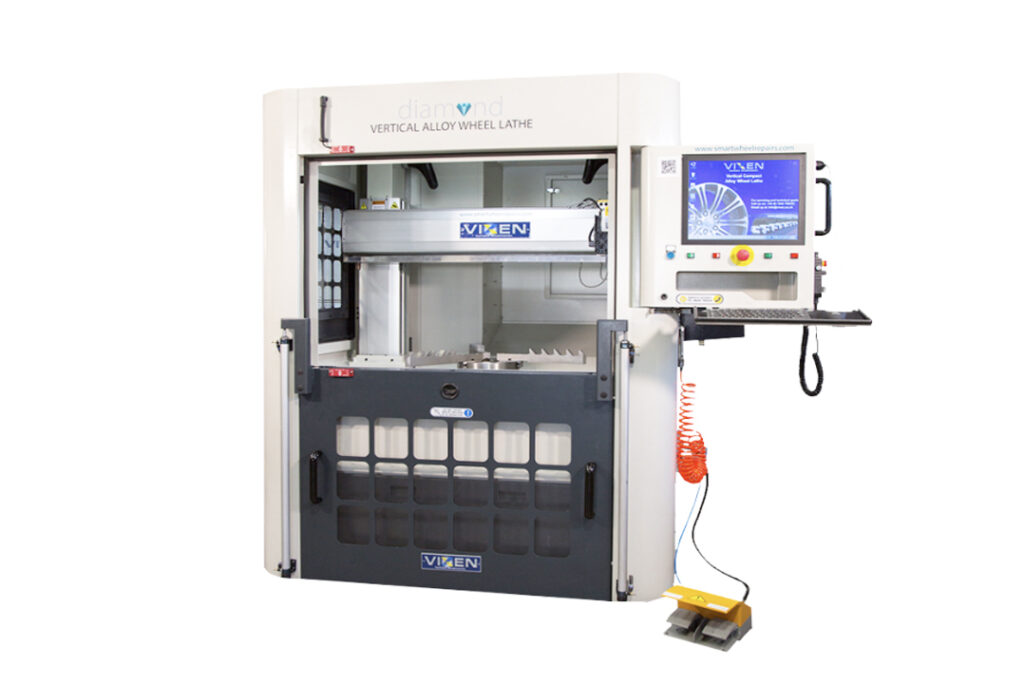

This compact lathe is the perfect addition to any workshop, with a footprint of 2mx2m and weighs only 1800 kilos, and has the ability to laser scan wheels in less than 30 seconds.
This lathe also features a Windows operating system making it familiar and easy to use. With every purchase of the lathe you will receive two days on-site training as well as our training guide and manual.
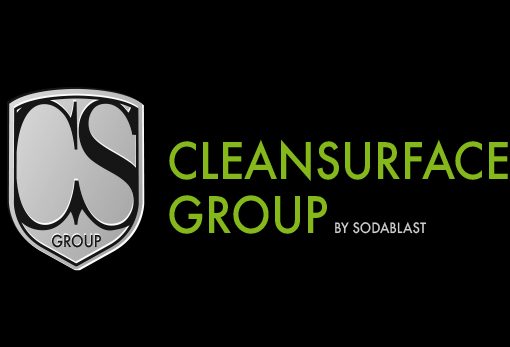
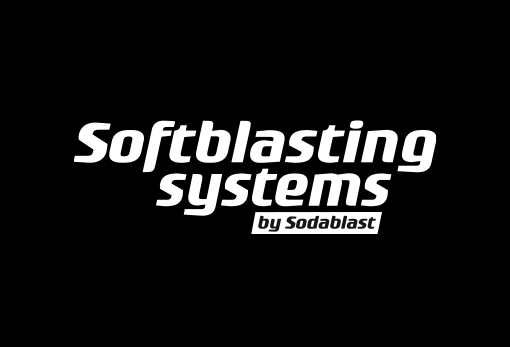

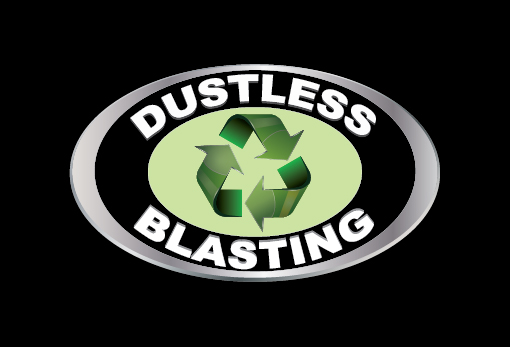
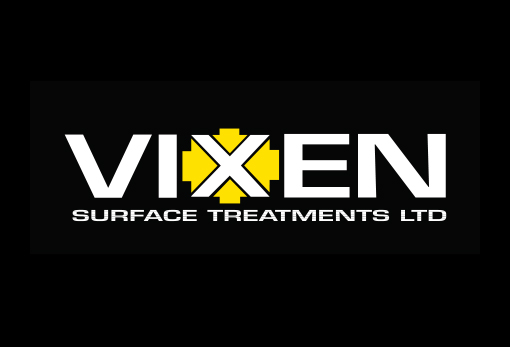
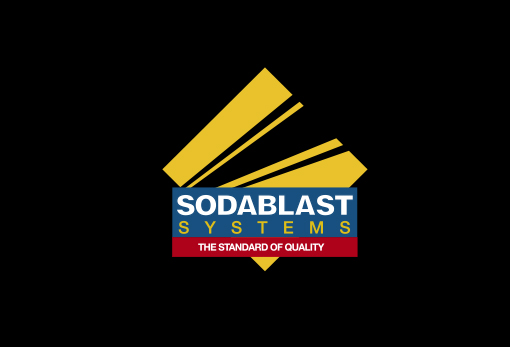